Page last updated on September 7, 2021 at 11:23 am
For more information, please contact
Ryan Hillenburg, Apprentice Master Mechanic, 812-349-3494 hillenbr@bloomington.in.gov,
Frank Robinson, Master Mechanic,812-349-3494, robinsonf@bloomington.in.gov
The Challenge
As part of the City of Bloomington’s plan to allow Kirkwood Avenue - a popular shopping and dining destination downtown - to be closed to motorized vehicles from time to time for events, 100 non-mechanical temporary bollards were installed at the intersections.
Bollards are short vertical posts that prevent motorized traffic from entering an area and allow the street to be transformed into a bicycle and pedestrian-friendly boulevard. When not in use, a 35 pound cast iron filler sleeve resides in the ground position to allow vehicular traffic to pass over the bollard locations within the street surface. In order for bollards to be installed, they need to be unlocked, lifted out of the ground, locked in place, and covered with a yellow plastic sleeve.
Working in collaboration with the Kirkwood Business Association it was decided to place the bollards every Thursday at 12pm and remove them on Monday’s at 7am through the last weekend of September. It takes 6 members of staff about 30 minutes to remove ground filler sleeves, place barricades, and install bollards and signage. Currently we are only closing three of the five blocks that are fitted with the ability to be blocked off individually, utilizing 34 of the 100 bollard positions.
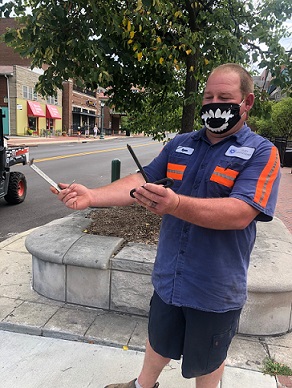
Shortly after the bollards were installed, staff realized that the standard tools used to remove the ground sleeve fillers were inadequate and required bending to unlock the sleeve filler, then lifting from a bent position to raise the sleeve filler and lock it in place. Each of the ground sleeve fillers, weighs 35 pounds. Staff were bending and lifting from a bent position 64 times/week (once to unlock/lift/re-lock, another time to unlock/lower/re-lock).
The Idea
Michael Large - Public Works Special Projects and Operations Manager - watched staff bending over multiple times and lifting from a vulnerable position and worried about the potential for back injury. Michael contacted Fleet Maintenance Manager Jason Speer about whether his staff might fabricate a longer tool that would prevent staff from having to bend over to do their work.
Jason recommended that Michael consult with Ryan Hillenburg and Frank Robinson. Ryan and Frank are well-known for their problem-solving prowess and their ability to create custom parts that are becoming more and more unavailable during the pandemic.
Ryan and Frank went out to observe how the staff were working with the existing tools, understood the problem that Michael wanted to solve, and created a prototype. They asked staff to use the prototype, got feedback from the Street staff as well as from the Fire Department (who might need to quickly remove bollards to respond to a fire in the area) and fabricated a second prototype.
With feedback from the eventual users of the tool, Frank and Ryan created version #2 of the tool and distributed it to the Street and Facilities crew as well as every truck in Station #1. (Special thanks to Battalion Chief Tania Daffron for training the Fire Department units in the use of the tool!) The second prototype features the lock/unlock mechanism on one end of the pole, and a lift mechanism on the other.
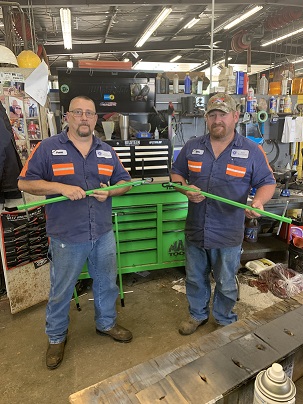
The Cost
Ryan and Frank were able to create six of these new tools for just $34 total! That’s less than the cost of a fancy Starbuck’s drink per tool!
The Benefits
Working with the fleet maintenance staff, Ryan Hillenburg and Frank Robinson designed and fabricated a better tool in less than 48 hours. The new design allows workers to lift the 35 pound load while standing upright using the strength of both arms and legs, instead of straining their backs.
Since there is no comparable tool, it is difficult to say how much money was saved by fabricating the tool, but if one could be found, you can bet that it would cost more than $6 per tool! And, of course, Ryan and Frank’s tools have improved the safety and wellbeing of the crews responsible for this work by reducing the potential for back injury using the old way.
The team would like to thank their manager, Jason Speer, for allowing them the autonomy to collaborate with those on the ground to make the task easier and safer for everyone involved.
Metadata
City Department(s): Public Works, Fleet Maintenance Div, Street Div, Facilities Maintenance, Fire Department
City Point of Contact: Ryan Hillenburg, Frank Robinson
Partner(s): N/A
Partner(s) Point(s) of Contact: N/A
Type of Innovation: Mechanical
Date Implemented: July 2020