Page last updated on September 23, 2020 at 9:19 am
For more information, please contact
Ryan Hillenburg, Apprentice Master Mechanic, 812-349-3494, hillenbr@bloomington.in.gov
Frank Robinson, Master Mechanic, 812-349-3494, robinsonf@bloomington.in.gov
The Challenge
As part of the City of Bloomington’s plan to allow Kirkwood Avenue - a popular shopping and dining destination downtown - to be closed to motorized vehicles from time to time for events, 100 non-mechanical temporary bollards were installed at the intersections.
Our bollards are short vertical cast iron posts covered by heavy brightly
colored housings that prevent motorized traffic from entering an area and allow the street to be transformed into a bicycle and pedestrian-friendly boulevard.
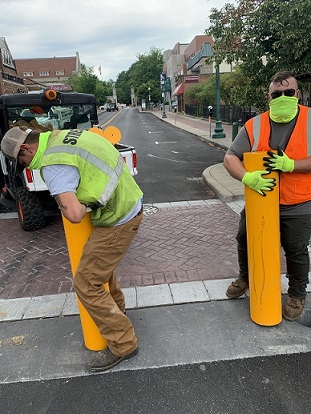
When not in use, the posts rest below the surface of the street and fill the hole; the heavier housing is stored in an adjacent lot. Each housing unit weighs 125 pounds and needs to be lifted off of the racks, transported to the location where they will be installed, and lifted onto the posts when the bollards are in use. Working in collaboration with the Kirkwood Business Association, the Public Works Streets and Facilities Divisions are responsible for installing the bollard housing on Thursday evenings and removing them on Monday mornings through at least the last week of September.
So, each of the 34 bollards actively in use is lifted four times each week: lift off the rack, lift onto the concrete post, lift off the concrete post, lift back on to the rack.
Special Projects and Operations Manager Michael Large observed the Public Works Street and Facilities crews struggling with these unwieldy bollard housing units every time they needed to be installed and worried for the safety of the crews.
The Idea
Through a recommendation by Jason Speer - Manager of Fleet Maintenance - Michael had previously worked with two members of Jason’s crew - Ryan Hillenburg and Frank Robinson to design and fabricate a rack for the bollard housing units. He knew that Frank and Ryan were master problem-solvers and was eager to get their thoughts about how they could make the installation of bollard housing safer for the crews.
After observing the installation process, Ryan and Frank set about creating a prototype tool that would grab the bollard housing unit and more easily allow it to be lifted and placed atop the concrete post. The prototype was tested with the crews on the street as well as with Fire Department staff from Station 1 downtown who would need to quickly uninstall bollards in case of emergency.
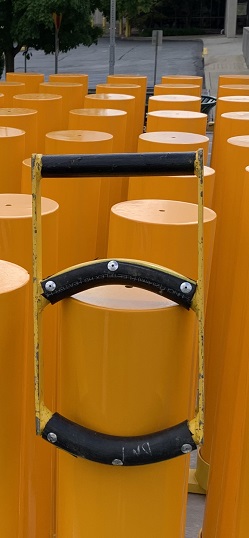
With feedback from the eventual users of the tool, Frank and Ryan created version #2 of the tool and distributed it to the Street and Facilities crew as well as every truck in Station #1. (Special thanks to Battalion Chief Tania Daffron for training the Fire Department units in the use of the tool!)
The Cost
Ryan and Frank are able to fabricate the tool for a mere $6/tool!
The Benefits
Using this new tool, Ryan and Frank saved the crews responsible for installing the housing sleeves time, frustration, and potential injury. Since there is no comparable tool, it is difficult to say how much money was saved by fabricating the tool, but if one could be found, you can bet that it would cost more than $6 per tool!
The team would like to thank their manager, Jason Speer, for allowing them the autonomy to collaborate with those on the ground to make the task easier and safer for everyone involved.
Metadata
City Department(s): Public Works, Fleet Maintenance Div, Street Div, Facilities Maintenance, Fire Department
City Point of Contact: Ryan Hillenburg, Frank Robinson
Partner(s): N/A
Partner(s) Point(s) of Contact: N/A
Type of Innovation: Mechanical
Date Implemented: July 2020